Understanding the Cement Industry!!
- Madhav Arora
- Jul 17, 2019
- 6 min read
Updated: Jul 17, 2019
You may have come across the taglines- "bhaiya ye deewar tut ti kyu nahi hai, ambuja cement se jo bani h!"; "Bangur cement!! sasta nahi, sabse acha" etc but have you ever wondered how these cement companies operate & generate return for their investors!
Well, today's discussion is about the same.
The article is a modest effort to build a basic idea in regards to the cement companies incorporating following points-
1) Process- How is cement manufactured?
2) Understanding the industry & sector specific fundamentals
3) Key ratios
4) Upcoming opportunities
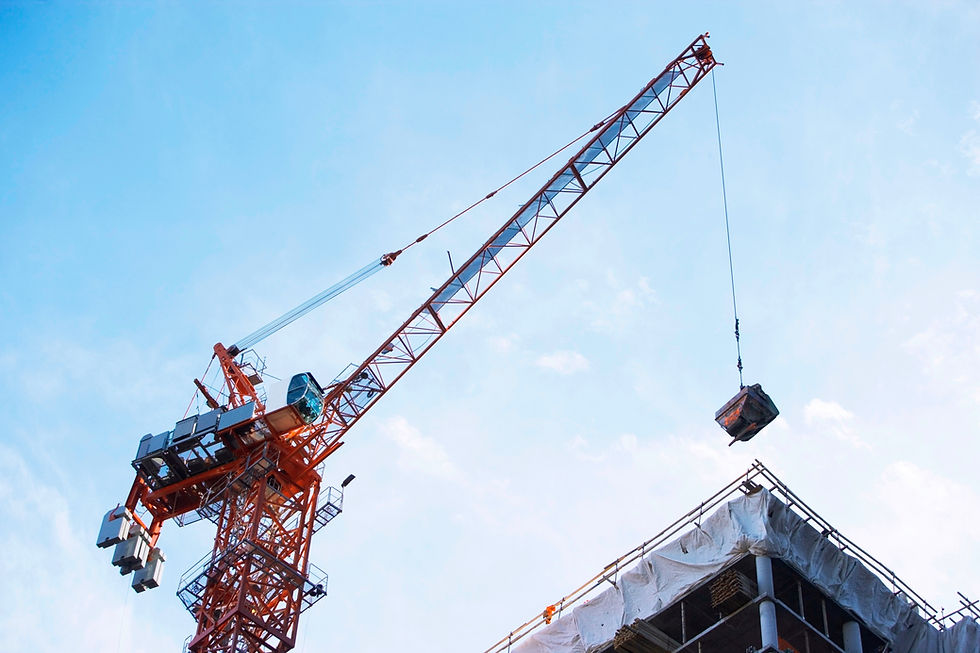
1) Process- How is cement manufactured?
It's really crucial to comprehend the modus operandi i.e the process of any industry. The basic understanding of the whole process helps you gain intimate perspective about (among other things) business model, best industry practices, inherent threats & upcoming opportunities, whether the industry is labor oriented or CAPEX oriented, extent of government intervention, pricing power enjoyed by suppliers, bargaining power enjoyed by customers etc.
To start with, "limestone" is the basic raw material for producing cement. Now, the question arises what is limestone & from where do cement manufacturers get that. Limestone is a natural mineral extracted from limestone mines. These mines are allotted & leased out by government to companies through auctions usually for a term of 99 years.

The limestone is then heated at certain temperature to produce a substance known as "clinker".
The fact to be appreciated here is that the companies which have got limestone mines on lease have an edge over companies which don't as limestone can not be directly purchased & therefore clinker can not be produced. i.e Clinker producers need to have their own mines.
In a nutshell, cement players which don't have their mines, buy clinker from other players but this scenario is really rare.
The next step is "grinding" which involves grinding clinker with certain other kind of materials like gypsum, fly ash or slag (explained below) to ultimately produce cement. The different grades of cement depend upon different levels of clinker, gypsum, fly ash and/or slag in the whole composition. Lesser clinker would mean lesser strength & vice-versa.
a) Gypsum is a natural mineral.
b) Fly ash is a by-product of Thermal Power Production. Most power producers want to dispose of fly-ash and one of the ways is by selling it to cement manufacturers.
c) Similarly slag is a by-product of Steel making process and is often sold to cement makers.
So, companies have two options-
(i) Make cement in the areas where limestone is available and the ship the finished good to those parts of country that want cement, or
(ii) Make only Clinker in the state where limestone is available, and then do the grinding of clinker in the region which requires cement.
A unit which does both grinding and clinker manufacturing is called an "Integrated Unit". A unit that does only grinding work is called "Grinding Unit".
2) Understanding the industry & sector specific fundamentals
I'll draw out the facts & figures in points to make it easy to read & understand-
(a) Some figures for starters-
(i) India is the second largest cement producer as well as consumer after China.
(ii) Our country has a capacity of 500 million metric tonnes (MT) & utilization on an average remains about 65% which is 325 MT.
(iii) Production for FY 2018-19 was 337 MT as compared to china's humongous production of 2400 MT.
(iv) Consumption for FY 2018-19 stands at 328 MT.
(v) 4 groups hold 50% of domestic market share- Aditya Birla, Shree cement, Dalmia, Holcim Lafarge
(b) Cement is a pure commodity due to lack of brand differentiation [reasons for same mentioned in point (c)], hence the sector is cyclical & selling price is governed by demand & supply. Also, there's a high degree of correlation between GDP growth rate & growth in consumption of cement (cement consumption grows @ 1.2 times the GDP growth as per researches & data)
(c) Cement can be sold to sets of customers-
(i) Retail Customer (Trade Segment)
As far as the retail customer is concerned, cement is a "push market industry" like the FMCG's, so whoever is able to push its product first to the customer, will be able to successfully sell it. The reason being, at the end cement is a commodity & a layman doesn’t differentiate between different brands. The lead sales influencer is your architect, builder or the shopkeeper. He goes to buy cement only when he immediately needs it, and will buy whichever is immediately available or whichever cement's ad pops up on his TV, hence the catchy promotions & taglines. So it is important for a manufacturer that he is able to successfully push his product on the shelf of shopkeeper (ship it on time) and incentivise the shopkeeper enough (discount and commission) so that he sells your product.
(ii) Infra Customer (Non Trade Segment)
The infra projects buy cement in bulk as cement is the basic necessity for every structure. The category attracts lower margins as compared to retail customer as bulk quantity attracts heavy discounts.
(d) It's a CAPEX intensive sector.
(e) For a cement company to earn more, it can do one thing- reduce it's overall cost by reducing either the manufacturing cost or freight. Cement is bulky, hence handling this bulky material takes a lot of efforts. It occupies a lot of space and carries a lot of weight. Hence, higher the distance a cement bag travels, higher is the freight and handling cost involved & lower is the profit a manufacturer makes. So a cement manufacturer needs to optimize it's freight cost by managing locations in regards to production units i.e Plants, limestone mines, warehouses, location of end customer i.e dealer. Also, in my opinion, plants should be as integrated as possible to save the cost of transportation till the grinding units.
(f) Power & Fuel cost is an important area to look after which makes up for 30% of total cost. Power is needed to heat the limestone (as mentioned earlier) to form clinker. Conventional sources include Coal, Petcoke or Lignite. Now, petcoke is cheaper than coal but usage of petcoke leads to high maintenance costs of plants. Look for companies which are into non conventional & cheap sources of power like rice or coffee husk thereby reducing their costs & carbon footprint.
(g) Because cement sector is cyclical, it becomes critical to anticipate cyclical fluctuations. In order to study cycles, one needs to constantly examine the levels of actual capacity, capacity utilization & production. Since the past one year utilization has increased from 63% to 69% as demand is increasing too due to growth in sales but prices have not increased at the same rate as various players increased their capacities & production as well.
Carry out a separate research to examine capacity, utilization & production levels on a region wise basis as cement sector is not uniformly spread across the country.
Of the total 210 large cement plants in India, 77 are situated in the states of Andhra Pradesh, Rajasthan & Tamil Nadu. i.e South India me zyada concentration hai production units ki due to availability of limestone mines
Go for a particular co. in a region where its capacity is low but overall demand is high to achieve higher realizations. For instance, North-East.
(h) Housing forms 65% of the cement demand in India and hence this is the biggest demand driver. Housing has been growing at a steady modest pace even during lean period. The infrastructure sector (20%) adds or restricts the much needed growth. So one needs to judge uptick in demand and more specifically, the demand supply mismatch in the Micro Market where the Cement player is located (highlights the importance of region wise research). Industrial development accounts for 15% of demand.
(i) Since mines are allotted by Government, they typically give a right of mining (by charging a hefty sum). Companies capitalize this amount as an "Intangible Asset". Hence an analyst can quickly check the Intangible Assets section in Balance Sheet to know if a company has a limestone mine. This Intangible is depreciated on the basis of quantity of limestone extracted as a proportion of actual quantity of reserves existing. So one can actually do a reverse calculation to judge the life and quantity of reserves a company has in their mines.
3) Key Ratios
(i) I personally avoid ratios like Price to Earning (PE), Return on Equity (ROE) as cement is a capital-intensive industry and hence depreciation forms a huge part of the total outgo. Considering depreciation can lead to absurd conclusions based on comparison with peers due to different level of CAPEX in different companies.
I instead prefer Price to Cash Flow & Price to EBIDTA.
(ii) Earnings before Interest, Depreciation, Tax & Amortization/ ton
or (EBIDTA/ ton)
(iii) Look out for debt levels (Again because of high CAPEX involved), examine Debt to Equity ratio (D/E) & Interest Coverage ratio .
4) Upcoming opportunities
1) Smart Cities mission
2) Housing for all by 2022 initiative has been aggressively launched by the government. Tax incentives are being introduced to boost the same.
3) The Government plans to invest INR100 lakh crore in infrastructure sector over the next
five years as mentioned by the Honorable Finance Minister in the budget day speech. Around 1,25,000 km of road length will be upgraded over the next five years, with an
estimated cost of INR 80,250 crore. The fact to be appreciated here is that govt. has decided to adopt cement over bitumen for construction of roads.
4) Moreover, the per capita consumption of cement in India still remains substantially low at less than 200 kg when compared with the world average which stands at about 500 kg. In case of China, it is over 1,000 kg per head. This underlines the tremendous scope for growth in the Indian cement industry in the long term.
5) Look out for regions of high demand in terms of increasing urbanization & industrialization, infra projects.
Picture Credit- https://images.livemint.com/img/2019/07/09/600x338/cement-kbwD--621x414@LiveMint-bdf6_1562681029786.JPG
Comments